Towards more sustainable linear accelerators in cancer treatment
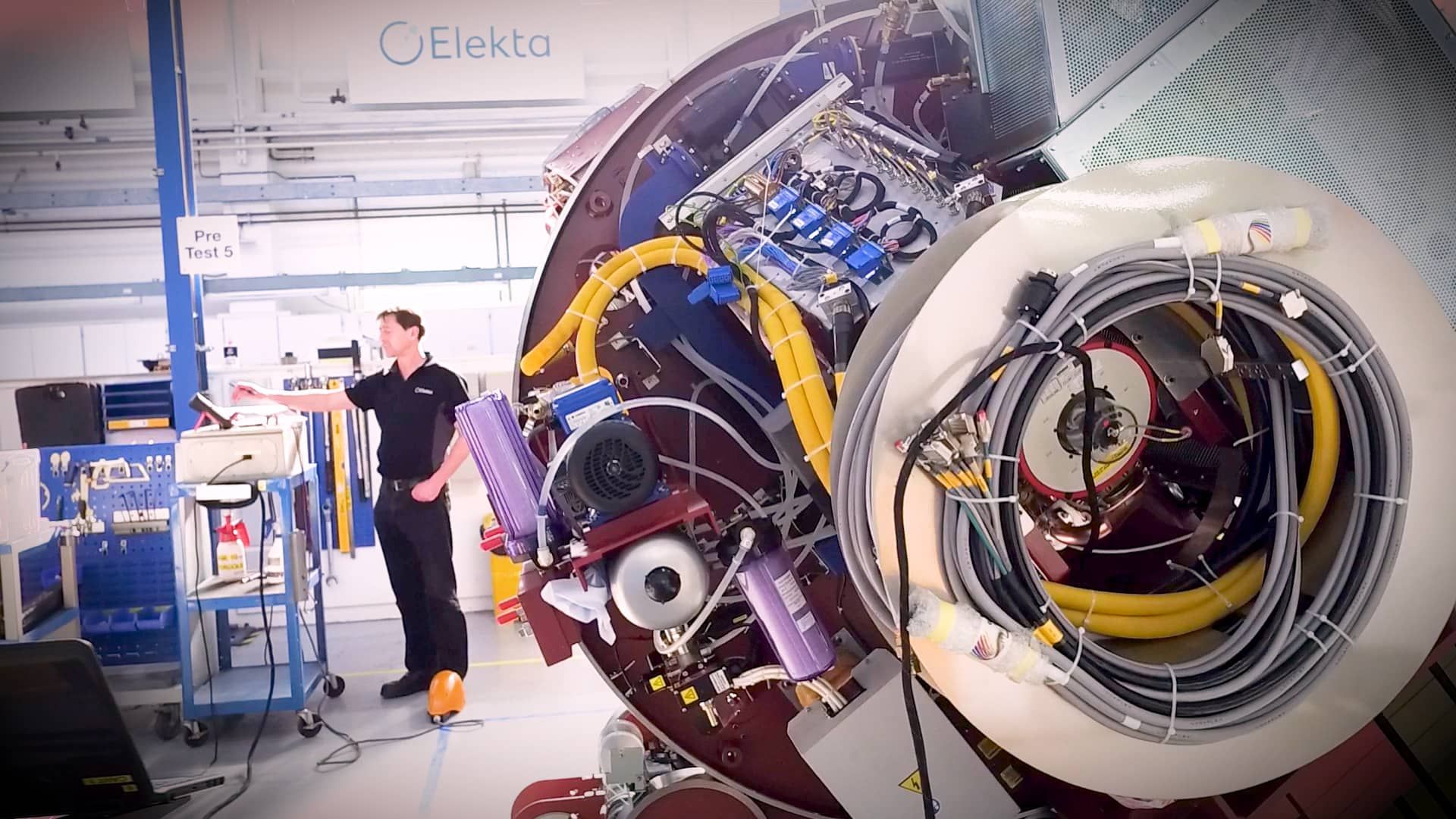
How Elekta is working to produce radiotherapy products that maximize positive impact
The radiation therapy industry is focusing intently on how to reduce the environmental impact of radiation oncology – prioritizing low-carbon strategies that cut greenhouse gas emissions and waste, incorporating environmentally conscious design principles and targeting zero waste to landfill, among other initiatives.
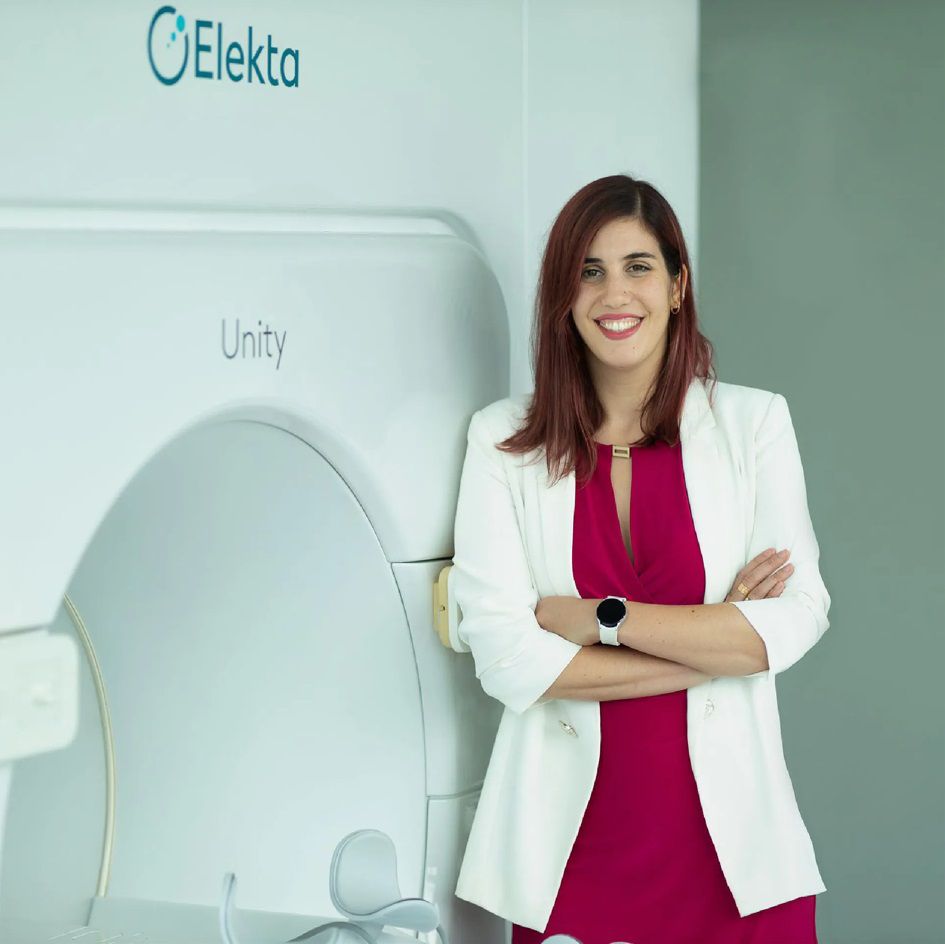
According to climate champion Rita Morgado da Silva, Hardware Systems Engineering Manager and sustainability lead for Elekta’s Global Product function, Elekta is actively supporting a more sustainable direction for the industry by minimizing the amount of material resources used, increasing energy efficiency, conscientious use of high emission materials, and enabling improved remote system diagnostics and service in an effort to decrease the carbon footprint connected to the treatments delivered.
“One of my life goals has always been to improve people’s quality of life and health,” says Morgado da Silva. “This is inherently linked with the ability to receive medical treatments as well as the reduction of waste and environmental impact. As the sustainability lead, I’ve been working on the implementation of environmentally conscious design practices – such as energy consumption, material selection and circularity – across Elekta’s radiotherapy portfolio.”
“We have put a lot of effort in the mapping of Elekta’s carbon footprint baseline and we now have a clear method on how to track the effects of the improvements we make in our products.”
Elekta has recently elevated its climate ambitions. Elekta’s carbon reduction plan has been set under the criteria of the Science Based Targets initiative (SBTi), which helps companies set science-based emissions reduction targets and provides independent validation of each company’s targets. “We have put a lot of effort in the mapping of Elekta’s carbon footprint baseline and we now have a clear method on how to track the effects of the improvements we make in our products,” Morgado da Silva says.
A focus on actionable and measurable design improvements
In the production of its linacs, Elekta has established design targets for projects and products, including minimizing the weight of new designs; identifying redundant or over-specified parts; optimizing the amount of shielding materials; designing new products to facilitate remote diagnostics; and reducing spare parts consumption.
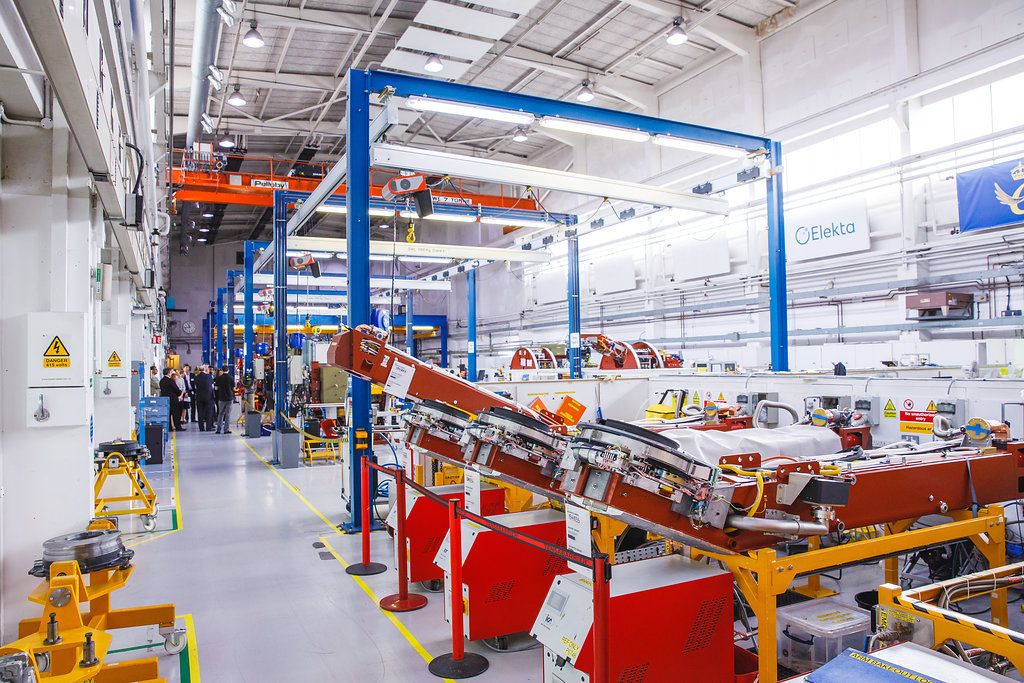
“We use finite element analysis – which is the use of calculations, models and simulations to predict and understand how an object might behave under various physical conditions – to optimize the mechanical design of our systems while ensuring we meet mechanical strength compliance requirements,” Morgado da Silva says. “For example, when designing a component for a linac, you need to comply with a certain safety factor. If you need a safety factor of four, there’s no need to design it with additional material that brings it to a higher safety factor, which increases the material mass and increases the weight of the linac. A higher weight means higher emissions as a result of not only primary sourcing and production of the part, but also increased emissions on transport.”
“Materials composition and their CO2e intensity were major consideration factors in the design of Elekta Unity MR-Linac,” she notes. Linear accelerators naturally produce high levels of radiation which require shielding – or a barrier between a radiation source and the area or person that needs to be protected – to reduce unwanted radiation from reaching the person receiving cancer treatment and surrounding areas. Due to their high density, two common choices of material used for shielding are tungsten and lead. “Since tungsten is a CO2e intensive material and lead a high-toxicity material, we wanted to minimize the use of both, and were able to successfully optimize placement of each using ray-tracing and Monte-Carlo simulation,” Morgado da Silva says.
It is important to note, however, that environmentally-conscious design is about reaching the right level of compromise between the amount and type of material used. For example, the Elekta Unity beam attenuator was redesigned from stainless steel to lead with the focus being to reduce the total amount of material used, resulting in the reduction of the total product CO2e emissions.
“For us to ensure we are tackling the right areas of the machine, we needed an overview and understanding of what are the biggest contributors to our emissions profile for the production and use of our Linac Solutions,” says Morgado da Silva. “This has been a true cross-functional effort over recent years to map our product and its lifecycle – and this will carry on developing as we introduce changes to our products but, also, as the way our customers use our machines evolves.”
“A recent UK study showed that our linac on average uses 50 percent less electrical power across all measured states compared to competitive products.”
Elekta is also constantly exploring energy saving opportunities for our products. “To produce high energy MV radiation, we inevitably need significant amounts of power,” Morgado da Silva notes. “A recent UK study showed that our linac on average uses 50 percent less electrical power across all measured states compared to competitive products. However, we can always do better and every little change matters. Hence, we are continuously focusing on implementing additional energy-saving opportunities for the benefit of both the environment and our customers. For example, a few years ago we implemented a new pump for the water-cooling system. This has reduced electricity consumption, providing more pumping power with the same electrical input.”
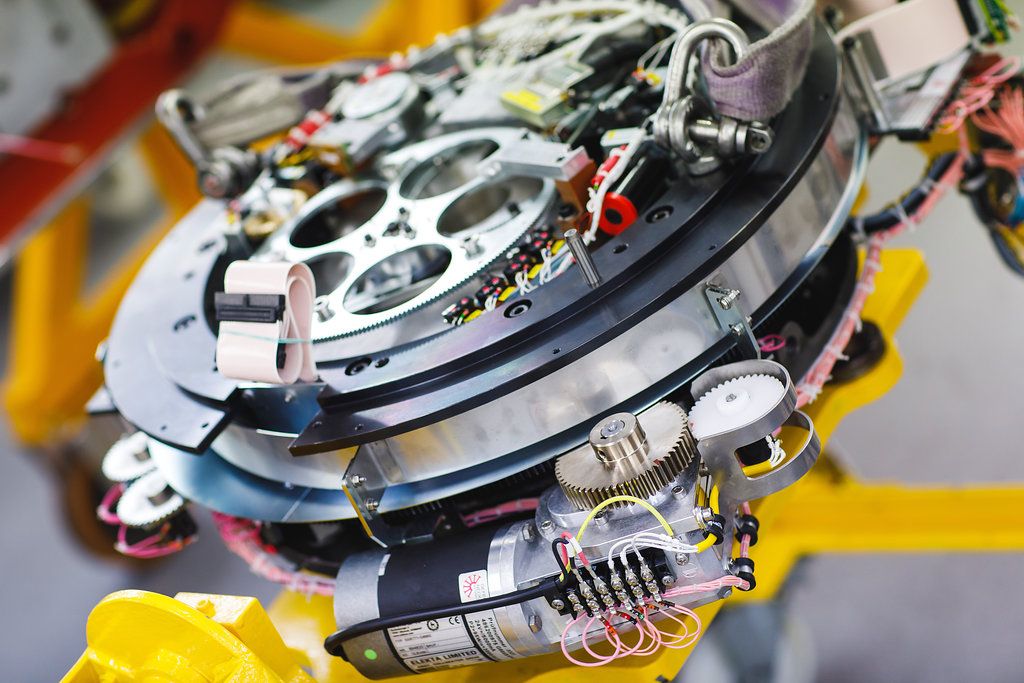
Innovation to lower power consumption is important from a sustainability perspective, as is the ambition of ensuring high patient throughput. “Elekta’s focus and roadmap focusing on optimization of workflows, reduced session time and the uptake on hypofractionation – which allows for patients to be treated in a smaller number of sessions - will allow a more sustainable approach to treating cancer. Our ultimate goal is to enable through our technology hospitals to treat as many patients as possible on each of our machines.”
Beyond linac manufacture
Elekta is continuously working to minimize the impact of shipping systems to customers. “Our analysis of freight modes showed that changing from air freight to sea freight results in a lower carbon footprint,” Morgado da Silva says. “Another aspect we take into consideration is our packaging. We are continuously working to develop better solutions whilst ensuring our machines and spare parts arrive safely to their destination.”
“With predictive and proactive maintenance, we’re able to better identify faulty parts, thereby decreasing waste and consumption of working parts.”
Another area of attention is predictive and proactive maintenance. “With predictive and proactive maintenance, we’re able to better identify faulty parts, thereby decreasing waste and consumption of working parts and, again, reducing the need for a field service engineer to travel to a customer site,” Morgado da Silva says. This is enabled by Elekta IntelliMax® – remote monitoring and machine diagnostics – which enables the access to real time data used in the building or predictive models, but also allows remote software distribution. Software updates are also distributed electronically and installed remotely, eliminating the need for physical media kits or site visits by an Elekta field service engineer.
Elevating sustainability as a company priority
“I’m excited that Elekta has elevated its sustainability ambition to the next level, and from a professional perspective, we’re responsible as engineers to think about sustainability and continuously raise awareness and action toward environmentally conscious design across the industry – for the benefit of all actors,” Morgado da Silva adds. “From a personal viewpoint, I care about the world we’re leaving to the next generation and the ability to be involved in making a difference in people’s lives and sustainability is like a dream come true.”
Learn more about Elekta’s commitment to a sustainable future.
LAROX231019