Making the machines to deliver state of the art cancer treatment for patients across the globe
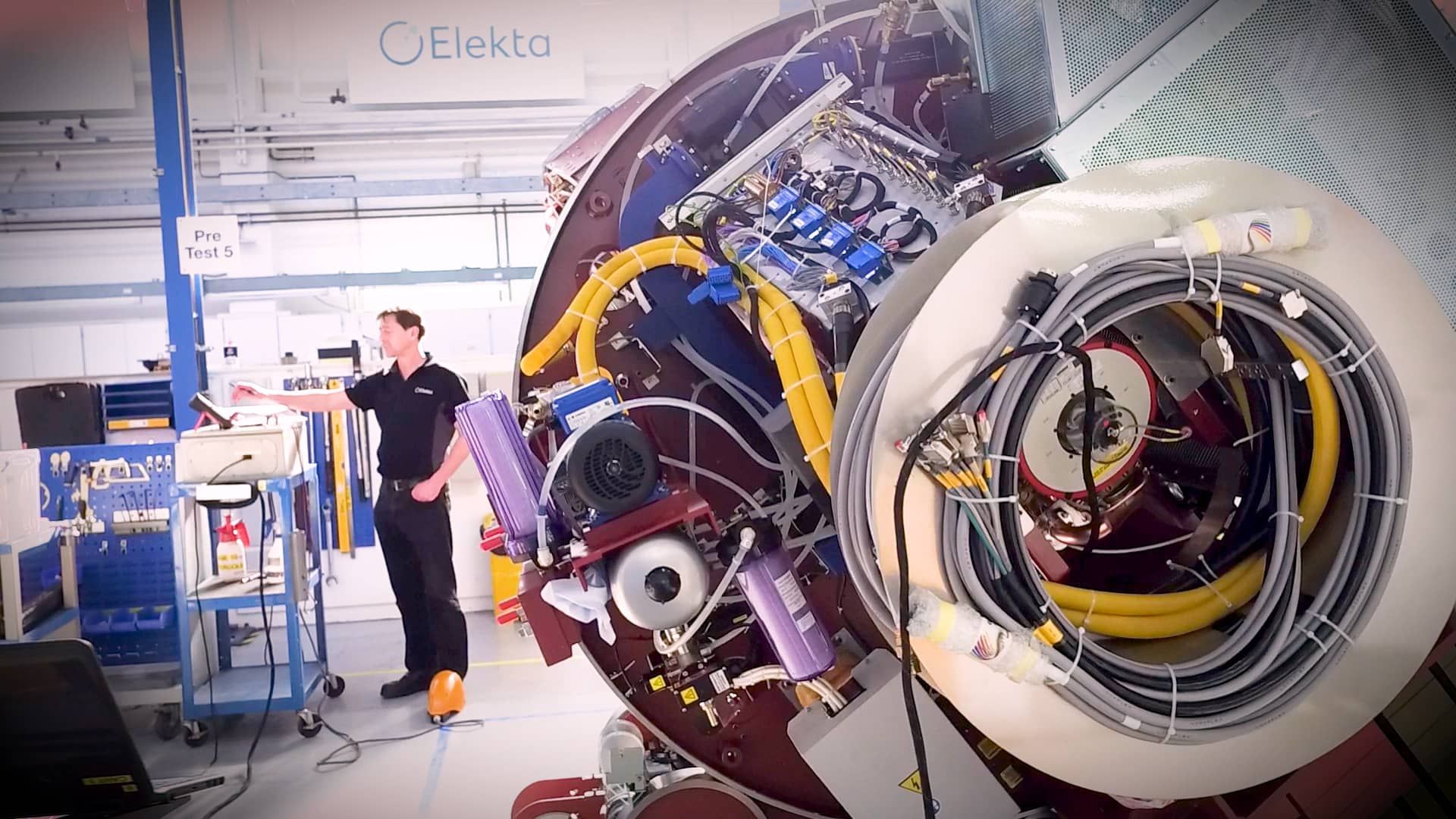
By Dave Remmer, Manufacturing Director, Elekta
Estimates put the number of cancer patients who lack access to radiation therapy at 300 million across the globe. Low- and middle-income countries have 80% of the global cancer burden but have access to only 32% of global radiation therapy resources.
Cutting-edge radiation therapy systems have critical roles to play in helping to address disparities and expand access to potentially life-saving care. At Elekta our ACCESS 2025 strategy is designed to provide access to radiation therapy by placing 800-1,000 new linear accelerators (linacs) in underserved markets.
“Experts at our manufacturing facility in Crawley are making life-saving machines to send around the globe and right now we have machine number 5,680 in production.”
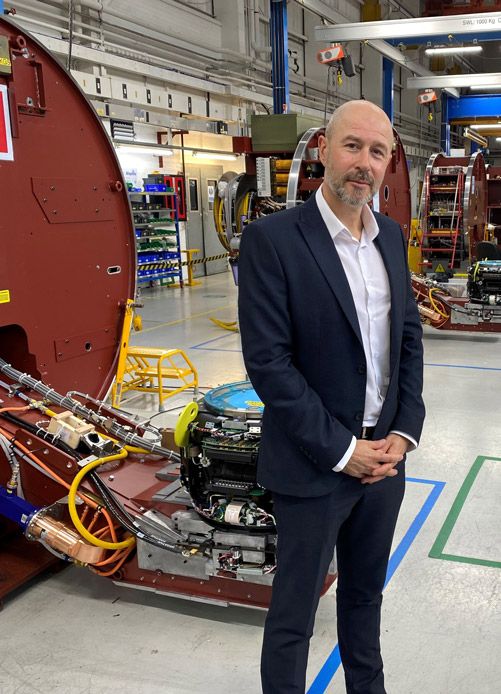
Experts at our manufacturing facility in Crawley are making life-saving machines to send around the globe and right now we have machine number 5,680 in production. This state-of-the-art manufacturing facility has made a machine for almost every country in the world – delivering Rwanda’s first machine last year.
Usually, there are 14 or 15 machines in progress at any one time and our largest annual output was 403 machines. The machines go through the five different stages of assembly and in total require 275 hours to build, test and dispatch. Each machine has around 60 hours of testing to ensure it has been set up and configured correctly to the customer requirements. We are 100% build to order, and every machine has the customer’s name labelled on it as it goes through the factory.
The linac itself, which includes the gantry, base, beam generation module and the beam shaping device, weighs just over 6.5 metric tons. Each machine is mainly made of fabricated and then precision machined steel with tungsten and lead used strategically for radiation shielding purposes. The waveguide that the electron beam is accelerated in is made from around 70 high specification oxygen-free copper cells that are machined and vacuum brazed together on site in Crawley. After a complex manufacturing process, they are tuned to the right specification by our specialist engineers. Many other components including printed circuit boards and other electrical and mechanical components are purchased from our list of approved suppliers selected for their expertise, quality, or geographical location.
Details of the serial numbers of the critical components, calibration information for test equipment and tooling, training records for all employees that have worked on the machine need to be recorded at every stage of the manufacturing process. This is because it forms part of the device history record, a regulatory requirement that must be complete and verified before the machine is signed off before leaving the factory.
“Every time a machine leaves the facility, we know that we have made a further contribution to improving access to potentially life-saving care.”
Finally, the machines are disassembled into five parts so they can be packed up and sent to their destination. It takes on average around 14 days from the start of the assembly process to the point where the machine leaves the site and starts its journey to the customer. Every time a machine leaves the facility, we know that we have made a further contribution to improving access to potentially life-saving care.