Austrian physicists save time and increase efficiency with Elekta QA solutions
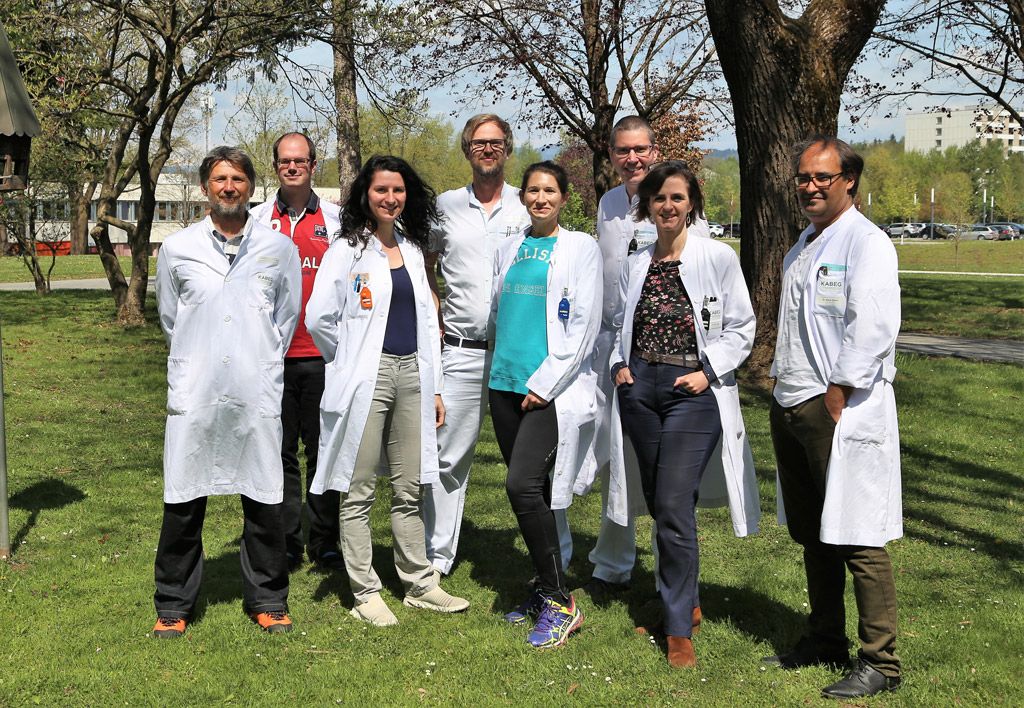
RT clinic leverages connected and automated machine QA software from Elekta
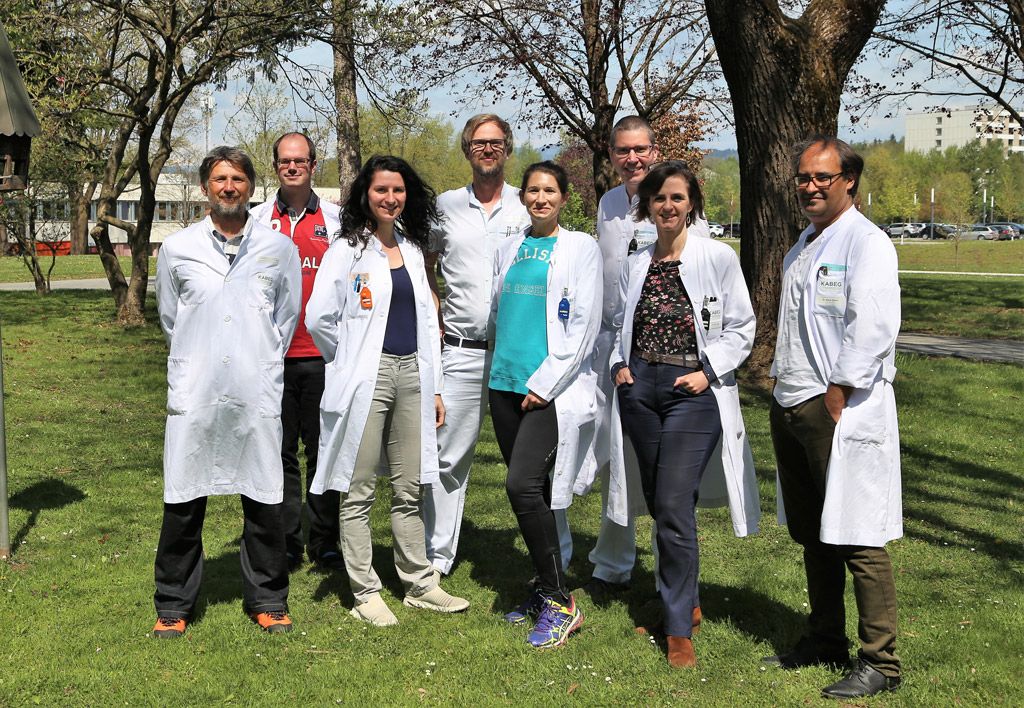
The Institute for Radiation Oncology at the Klagenfurt am Wörthersee Clinic in Austria is a growing and thriving radiotherapy department. Not only have they updated their linac fleet to four state-of-the-art Versa HD™ systems between 2015 and 2020, they have also recently decided to refresh and modernize their machine QA program, with the aim of making it more organized, efficient and paper-light.
Typical of a busy radiation therapy department, the physics team faced a range of challenges in terms of QA scheduling: Difficulties in allocating both physics time and time at the linac resulted in long out-of-hours working; some tests were manual and time-consuming, making them difficult to perform regularly; and there was a need for better task distribution and oversight within the growing team.
“Previously, machine QA in our department was quite chaotic, with lots of Excel sheets, paper signatures and folders.”
“Previously, machine QA in our department was quite chaotic, with lots of Excel sheets, paper signatures and folders,” comments Andreas Gmoser, medical physicist. “We wanted a software system that would help to make our QA program more systematic, and which would give us a better overview of equipment QA status. We also wanted software that would help simplify some tests.”
“We were attracted to Elekta’s machine QA solution because of its connectivity with Elekta linacs,” he continues. “This capability eliminates some of the most tedious aspects of QA for certain tests, such as uploading images to the software and operating the linacs manually. The ability to automate some tests is invaluable. We also liked that this platform could provide the departmental overview that we desired.”
“The ability to automate some tests is invaluable.”
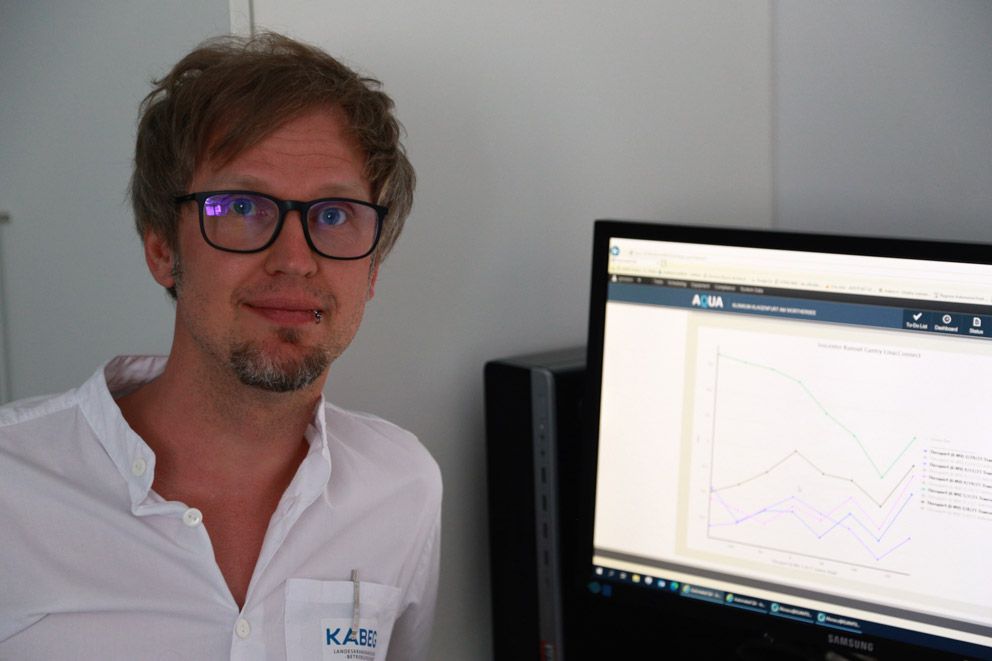
Easy and flexible implementation
“We began using Elekta Machine QA about a year ago,” Andreas says. “Installation and CAT was quick and easy. Then we began to customize installed tests and add some of our own.”
“This solution comes with a library of QA tests based on TG 142 recommendations,” he explains. “The first thing we did was to rename these tests and add some new ones, using simple scripts, to meet the requirements of Austrian standards.”
“Initially, we set up one linac with some simple tests and then, as we grew in confidence, gradually spread the scope of the solution within the department. We are now implementing the platform across our entire QA program, including all our previous QA routines.”
“We are now implementing the platform across our entire QA program, including all our previous QA routines.”
“The infrastructure of Elekta Machine QA is open, allowing you to adapt the software and create your own tests, so it is really customizable,” Andreas continues. “We created java plugins to allow us to import data from third-party QA devices and programmed additional tests specifically for our clinic, in java and xml. We also adopted some existing scripted tests we have been running, so that they are now running automatically within the software. For example, we directly imported our TPS QA into the system. This is now easy to run automatically on a daily basis, which makes it less likely to be overlooked and centralizes the results.”
Improvements to the QA program
Automation of certain tests, through connectivity with both measurement and delivery devices, enhances machine QA efficiency. The platform also reduces dependency on paper and folders by providing a centralized, easily accessible source of QA data. Its open, web-based design provides a valuable QA overview for authorized users, wherever they are, and allows easy monitoring of machine QA status within the organization.
“The thing I like most is its connectivity to our linacs,” says Andreas. “This is the only QA software package with this feature. It allows us to run tests automatically, which is really cool. This has made some of the tests much quicker and easier to perform and ensures that we can run them as regularly as we’d like. For example, the MLC QA test was previously very laborious and time-consuming, requiring numerous films to be made and analyzed. Now, this test can be performed automatically in minutes with just a few mouse clicks.”
“Now, this test [MLC] can be performed automatically in minutes with just a few mouse clicks.”
“Simplifying and automating tests makes it easier for staff to learn and perform them regularly,” he adds. “We can even add a description of the test to make sure people are clear about what to do. It is also possible to define and distribute tasks and, of course, the dashboard provides a good overview of machine QA status in the department. Everyone can see what has been done and what needs to be done, and there is less chance that something could be missed.”
Benefits to the department
“Since we have implemented Elekta’s machine QA solution, we have found that the whole department is more aware of QA,” Andreas comments. “We have gone from chaotic QA testing, where we only had time to do the absolute minimum, to a more modern, thorough and efficient QA program. We now perform tests regularly and in an orderly way, with all the test details and results stored in one place, not in various files and folders. This helps us to be fully compliant with Austrian standards and to be ready for our annual QA audits.”
Providing centralized, easily accessible QA data, it reduces the need for paper printouts and folders. The open, web-based design provides easy access, monitoring and maintenance of all machine QA throughout the department.
“The plan is that this change will help the department to reduce paper and even to go paperless in the future,” Andreas adds. “Previously, we were producing a lot of paper for QA, including printouts and signatures. Now everything can be stored digitally, with password-protected acceptance of results instead of signatures.”
“This machine QA refresh has freed up time for us to be more thorough and to perform other important tasks.”
“As physicists, knowing that QA has been performed at the right time and in the right way, having it all organized in one system gives us confidence in our department’s equipment, and maybe even helps us to sleep a little better at night,” he continues. “Some of the tests are so fast that we can check a calibration in minutes. This machine QA refresh has freed up time for us to be more thorough and to perform other important tasks. For example, we use the gantry run out test to calibrate our ExacTrac system. Previously we had to invest a couple of hours in a day for this test, which was difficult to schedule, but now it is easy to fit in and perform weekly.”
Future hopes
Having invested so much time in modifying and adding tests to satisfy Austrian regulatory requirements, it is encouraging that the team at Klagenfurt is willing to collaborate and share test scripts with other Austrian RO centers.
“We have already recommended this solution to other departments in Austria and we will be happy to share test scripts with them” concludes Andreas. “Our hope for the future is that they will also share development work and scripts with us, which will benefit our local radiation oncology community, saving time and effort for everyone.”
Learn more about our QA solutions.
LWBOX210712 v1.0